Technical Assistance Service
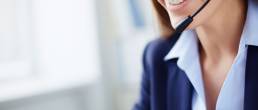
Services
We offer an efficient and global technical assistance service to customers during the installation and commissioning of the machines, including the resolution of problems, as well as any future incidents that may arise in order to optimise productivity and reduce downtime in industrial installations. In addition, spare parts and warranty services are included. Both the technical interventions and the availability.
- The stock of spare parts of both standard parts and expressly designed parts is guaranteed. Both the technical interventions and the availability of parts are practically immediate.
- Customer inquiries are answered within the first 24 hours and resolved within the first 72 hours.
- The availability is guaranteed during the first 25 years of any part that is part of the installations of the equipment.
- Technical assistance in case of maintenance and revision of the equipment is done by our own personnel, possibly thanks to the help of approved local technicians.
- The 90 percent of spare parts are standardized, that is, they can be provided locally, drastically reducing downtime and intervention, as well as cost.
- Technical interventions can be programmed to be carried out practically 365 days a year.
- All equipment is covered by warranty for the first two years of service.
Consulting
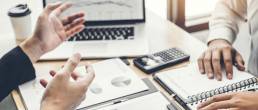
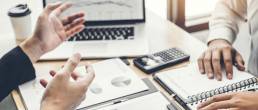
Services
- We have carried out more than 600 projects in the more than 44 years of activity. This experience is the knowledge base for the development of current and future projects.
The 44 years of experience in industrial processes in roasting, grinding, transport and silage are continuously applied in each development of our projects. The projects are personalized, therefore, they need to be evaluated and studied in detail by the technical team of each Client. For this, the constant flow of knowledge is essential, thanks to our technical training and consulting team. - The geographical location where the process equipment must be installed is a determining factor for the study of the project, since sometimes future Clients do not have detailed knowledge of what are the technical solutions available today. Our training and consulting allow us to evaluate and adapt our equipment so that it is the most appropriate solutions to your needs.
- We are first and foremost an engineering, so all approach to the projects is done with technical procedures, and on the basis of the equipment developed over the years, and these are adapted to the needs of the project. We do not work on catalogs, but on engineering.
- The staff of our technical team personally and regularly visits the Clients, in order to know first-hand what are the processes that are carried out, what is the use that is being given to the installed equipment, which sometimes is not the one that was originally designed, and with it studies of adaptability of these equipment are made for the new needs, taking into account for future enlargements.
- The technical assistance to our teams is carried out by our own technicians, possibly accompanied by local technicians. The start-up and training of the operators who are going to make use of our equipment is carried out by our own specialized technicians, not through intermediaries.
- Consulting and training services are available 365 days a year.
Innovation and R&D
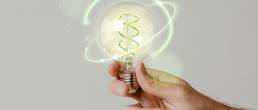
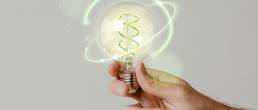
Services
- The designs of the process plants are carried out in our Engineering department. Therefore, all projects are customized and adapted to meet both current and future process line needs. Plant designs are based on the extensive experience of existing projects, and these are adapted to the requirements of the new project.
- The packaging section is the most dynamic part to consider in the design of a process plant. To this end, we are in permanent contact with both the Customer and the supplier of the packaging equipment, in order to adapt the design of the process line to the needs of the packaging machinery, and any needs in the future, such as the installation of new packaging equipment, format changes or increased packaging capacities. The location of the packaging equipment conditions the design of the project, having to adapt the transport and storage equipment if the packaging machines are located near or far from the process equipment.
- The roasting process is also different in each case, not only in relation to light and dark roasts, but also when roasting with additives, different product sizes and different mixtures. New advances in the studies of roasting processes allow us to adapt our roasters in order to achieve the desired results.
- Plant designs, silo capacities are a very dynamic part. With the new silo designs, the change of capacities and the change of the number of departments is easy to carry out, being able to be updated in a short space of time. The design of the silos allows these changes to be made quickly easily and economically.
- In each geographical area there are new specific regulations that need to be observed, not only in terms of process quality and product quality, but also those related to employee safety. Each project respects the existing regulations, and the most demanding ones are applied in all cases.
- Processes increasingly need to be faster and more efficient. To do this, the experience that is acquired over the years, thanks to a large number of installations that we carry out, allows us to know what are the points of improvement and efficiency that must be used for new projects. Roasting times are getting shorter and shorter, grain developments are larger, by higher sterilization percentages, higher milling capacities, degassing times are shorter, and transport distances and capacities from process equipment to packaging equipment are longer and longer.
- The development of the equipment takes absolutely into account the geographical uniqueness where the equipment will be installed, since each site has specific climatic and geographical conditions. The technical training of the operators is also unique, therefore, the equipment is designed so that they can be used more effectively and easily by the operators, and that these equipment can be 100% efficient under different operating conditions.
- The degrees of automation of the equipment are also different: although all the equipment is automatic, the access to the automation can be of different degree, from simpler presentations to avoid the erroneous use of the equipment, to more complete ones that allow a higher degree of personification in the use of the equipment. The degrees of automation are dynamic, that is, they can be adapted at any time during the life of the equipment.
- A large part of the projects that are carried out must respect the traditional methods of roasting, many of them preserved from generation to generation. It is possible to adapt the equipment so that these traditional processes are done effectively with modern equipment, allowing to fit artisan elaboration processes with modern technology effectively.
- Current process equipment has lower energy consumption compared to older models. Innovation studies allow that, in the future, these consumptions are even lower and more efficient, and that they are adapted for the use of renewable and clean energies.
- Equipment is increasingly being designed to be more robust and reliable during all years of service life. All equipment is designed so that the performance of the equipment is nominal during the first 25 years of useful life of the equipment, without the need for significant modifications.
Engineering and design
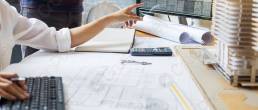
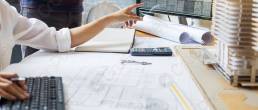
Services
- For the design of a roasting and grinding plant it is necessary the type of coffee which is intended the process to design. The equipment allows to process both pure or natural coffee, as roasted coffee adding sugar, gourmet coffees, coffees for HORECA or retail, for soluble coffee or coffee for capsule. To do this, plant processes and designs can be different with different configurations and need different care to take into account in the design of the plant. In the case of cocoa, cereals and beans, the equipment and its operation are adapted to what will be the subsequent process, either pressing, grinding, or the direct packaging of the product.
- The types of packaging that must be used in the plant condition the design of the process line: from packaging in capsules, vacuum packaging, in cans, in flexible packaging bags (horizontal and vertical), in bulk, the packaging of ground coffee, roasted coffee beans, or cocoa and roasted beans require different configurations to take into account, both in the packaging capacity required and in the care of the product so that it preserves all its qualities before the packaging process.
- The process lines are configured and designed in a personalized way, even to obtain the same product, depending on whether a simple and flexible configuration is needed, or more sophisticated and demanding. To do this, the needs of the project and the installation area of the equipment are evaluated, so that the process line has the maximum performance.
- Especially with coffee, roasting and grinding has not always been processed in the same way over the years at different times and in different generations. The roasting and grinding processes have been evolving, since consumption habits are also different. Both roasters and mills have been and are being adapted so that they can meet these new demands that the market demands and are in continuous development for the next needs and new forms of consumption.
- The facilities can be designed complete, from receiving the grain to be processed to the packaging; or partial, because they must be part of an extension of an existing line. The engineering study allows adapting this new equipment to existing facilities, being or not manufactured by us, in order to harmonize the production process of existing equipment and that there are no incompatibilities.
- The design of the plant must also consider the availability of space from where the equipment has to be installed, both in surface and height, as well as the geographical location, and the maximum use of the available space. The study of the project is always personalized, minimizing the use of space required for the installation of the equipment, and that this location allows in the future to make extensions, with similar or greater capacities, with equipment that processes the same type of product, or different products.
- All the plants are designed to, in the future, be modernized, or be expandable, either through parallel lines or capacity expansions of the different elements that compose it. Modernization not only affects the manufacturing process of the product, but also the adaptation of new legislation and regulations of mandatory application.
- The design of the plants is based on the complete knowledge of the final product that has to be elaborated. To do this, periodic visits are made to the customer in their process plant and a detailed study is made of what is the product to be elaborated, what is the current process and what are the improvements that must be implemented, so that with a more modern technology the same product can be repeated, or even evolve it if required.
- The development of the project is done together with the Engineering, Maintenance and Production teams of the Client. The projects are reviewed and customized in every detail, thanks to the participation of the Client in the definition of the needs, allowing our engineering team to develop the solution that best meets their needs.
- Environmental regulations are continuously updated, becoming increasingly broad and demanding, thanks to the increasingly pronounced environmental awareness. The projects observe maximum energy savings, minimize emissions as much as possible, contemplate the recycling of water, and the use of renewable and clean energies. All projects use the technical solutions that allow the most demanding environmental goals, and that are adaptable for future needs.
- The process plants and the equipment that compose it not only elaborate and produce satisfactorily the desired final product, but they achieve it by adapting to the Client's work methodology. The work habits and methodologies of the operators are taken into account, and the available resources, in order to facilitate the use of the equipment, and that they have the maximum performance.
- Increasing energy efficiency is mandatory in the designs of new projects. For this, heat recovery systems are incorporated, installation of low energy consumption motors, use of renewable energy sources, or rationalization in the use of equipment, which remain at rest when their operation is not necessary. The designs and manufactures of the equipment avoid the use of materials with unnecessary energy consumption.
- The teams are obliged to take care of the food safety of the product they process, as well as the safety of the operators who operate the equipment, in order to comply with the required regulations, and respect the most demanding quality and safety standards.